One of the most important things that keep a warehouse operation smooth and well-oiled is…
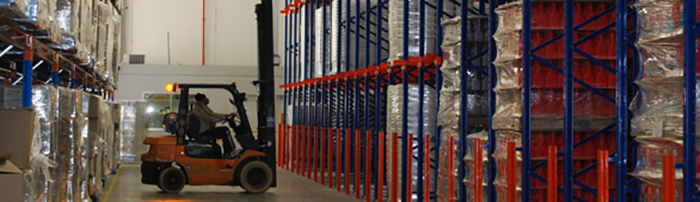
Is Drive-In Pallet Racking the Right Option for You?
Although you can enjoy denser storage levels when using drive-in pallet racking, this option may not be suitable for your particular warehouse environment. In some cases, you may get results that are just as satisfactory by converting a few existing racks to a double-deep system and installing a few extra racks instead. As a result, it is imperative to take the points below into consideration before making your final decision.
How Deep Can Drive-In Rack Lanes be Made?
It is important to remember that there are a few differences between the various concepts amongst the available Australian drive-in rack brands on the market.
However, the Colby brand is the only one currently available that conforms to the FEM 10.2.07. Additionally, the lane depth of this brand is usually only limited to the practicality of your warehouse design and current layout of other pallet racking you may have. In the end though, there is no definite answer regarding how deep the lanes can be, because factors such as stock turn, forklift operations and warehouse operations will all need to be taken into account.
Consider Occupancy Rates
Low rates of occupancy (between 65% and 75%) will benefit most from using drive-in pallet racks. In most cases, this is because of deficient accommodation strategies that can be forced through unwanted inventory movements and/or storage systems that have been poorly designed to begin with. However, occupancy rates like these can be improved substantially when smarter analysis is undertaken to improve on an existing warehouse layout.
Here’s an example: One lane of drive-in rack that has been designed as 4 pallets deep and 3 pallets high will hold 12 pallets in total. One SKU has been allocated to one lane and the regular inventory count on it is 10. Owing to the fact that drive-in racking works on a last-in first-out system, a warehouse manager will try to empty the lane before new stock needs to be packed away. However, when all attempts fail to move all of the stock and 10 pallets of new stock arrives as well, a second lane will have to be occupied. This will then result in 14 pallets being present in a space designed for 20 pallets – equivalent to a 70% occupancy rate.
The best way to improve scenarios like those mentioned above would be to implement a combination of drive-in racks with varying lane depths or alternatively, a mix of double deep, drive-in and/or selective racking. Doing this could help boost occupancy to as high as 90%.
Potential Disadvantages of Drive-In Pallet Racking
Although drive-in racking provides the most economical storage option in small to medium size warehouses, there are still a few limitations that need to be considered.
No natural stock rotation exists in drive-in racking because last-in first-out operation is forced. In addition, drive-in rack provides limited selectivity because each lane is only occupied by a single SKU during normal operation. Many European pallet designs don’t cater for drive-in rack systems, and they also require the use of compatible forklifts. When rack protection equipment is inadequate, drive-in racks can be more susceptible to damage during operation as well.
If you are a warehouse manager or you would simply like to learn more about drive-in pallet racking system, feel free to contact us today.