One of the most important things that keep a warehouse operation smooth and well-oiled is…
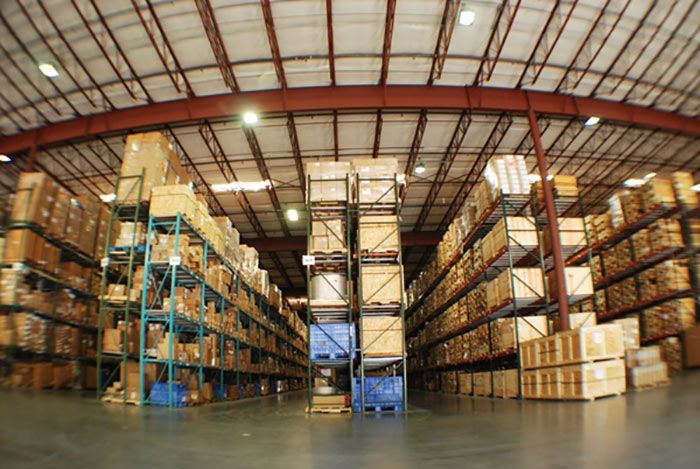
3 Methods that can Help Improve Warehouse Outcomes
- Analyze and Improve Turnover
Turnover refers to how long it takes to sell stock, and it can apply to a single SKU (Stock Keeping Unit) or all stock items. Good warehouse managers analyze turnover regularly and do everything possible to reduce the holding of items that are slow movers. When unused SKUs are stored for too long, the chance of recovering the amount spent on them initially is reduced substantially. Another area where a loss will be experienced is in the cost of wasted warehouse space – only storing fast-moving SKUs could result in less warehouse space being needed.
Try this Exercise Out
Although many warehouse managers would be thrilled at the prospect of being able to perform a full stock rotation every 90 days, it was recently noted that one warehouse in particular had a policy that entailed no stock being left on shelves for more than 14 days. If a particular SKU hadn’t sold within this time, it was removed and added to others that had also not sold during this time and all of it was put on sale within the next week. Whatever stock didn’t sell at sale prices was sent back to suppliers for credit. Anything that was non-returnable or that didn’t sell at sale prices was donated or discarded. This method enabled all stock to be rotated within a maximum of 30 days.
See how much Slow-Moving SKUs can cost
Determine how many cubic meters of your warehouse are dedicated to stock storage and divide it into the annual real estate cost. Be sure to include aisle space, common areas and access points as well. The end result will be how much each cubic meter of space costs per year. Multiply this by the amount of cubic meters that redundant stock is occupying and it could amount to thousands of dollars.
- Optimize SKU Locations Regularly
‘The Law of the Vital Few’ (also referred to as the 80/20 Rule and Pareto’s Principle) is a great way to optimize product locations in a warehouse. The concept surrounding this is that 80% of a warehouse’s SKUs will be subject to just 20% of overall warehouse movement or activity. As a result, it is recommended to keep the fastest-moving 20% of SKUs in the most convenient location for receiving and dispatch purposes.
- Peruse Warehouse Activities
In most warehouses, there are areas of activity that are highly inefficient, which wastes time and money. Although encouraging communication with everyone concerned could result in affordable solutions being found, there may be instances where it will be necessary to call in the experts. One of the best ways to get the necessary help is to set up video equipment in a warehouse, as this will help determine which processes or methods are flawed. Once this has been done, a range of solutions can be considered to help make the warehouse in question more efficient than ever.
Once a warehouse’s space has been properly optimized and the most popular SKUs have been stored in the most accessible areas, efficiency levels will increase substantially. If you are manager or company owner who wants to improve warehouse efficiency levels in your environment, contact us today.